Any LEGO enthusiast knows the importance of good build instructions. Any housing project relies on detailed plans by architects. Building a space mission is no different – before construction work can begin, there must be a functional blueprint to show how you can achieve your goal within the budget, with the resources available and within your deadlines. In fact, given challenges for materials working in the harsh space environment and the cost implications of additional size and mass at launch, anyone building a space mission will need to rely on the accuracy of that blueprint – down to the very smallest nut and bolt.
Since early March this year, partners in the Twinkle consortium from all over Britain have been working to produce such a blueprint in what’s known as a ‘payload study’. The payload is the instrument needed for a satellite to complete its scientific mission – in this case, the telescope and spectrometers that Twinkle will use to look at exoplanets atmospheres.
Different partners are responsible for the detailed design of different parts of the payload: Rutherford Appleton Laboratory for the telescope and cooling system; the UK-ATC for the infrared spectrometer, UCL’s Mullard Space Science Laboratory for the shield from stray light and thermal radiation from both the Earth and Sun, SELEX, Cardiff University and UK-ATC for the detectors; and Cardiff University and UCL for the pointing systems. We are also using hardware developed by the Open University for the visible light spectrometer. Obviously, this requires a lot of collaboration between partners to ensure that all the payload components will fit and work together. Thus, over the past few months, there have been a lot of meetings and fortnightly phone conferences to make sure everyone involved is up to date on progress and any change of plans.
Every one of these partners faces multiple choices about which components to use for Twinkle’s payload. We can choose ‘off-the-shelf’ components – ones that have already been used in space missions and have a track record in working in the harsh conditions of space. Or we can instead opt for new – perhaps lighter or cheaper – components that have not yet been tested. Of course the new components can (and have to be) be tested at low temperatures and vacuum conditions, but that takes both time and money.
As our Payload Lead, Dr Giorgio Savini, explains: it’s not always the thing you expect that causes a mission to fail. It could be something as simple as a mechanical hinge that starts acting differently under the stresses of the space environment.
Ultimately the choice comes down to how much components cost, how soon they can be made ready and, most importantly, which is the best fit for Twinkle’s scientific goals. If the mission needs to be able to pick out specific wavelengths to detect molecules in an exoplanet’s atmosphere, the components that can do this the best, or most closely, are chosen. It is not always an easy choice!
However, it is the ability to take these off-the-shelf components, and the speed at which we are developing new ones that allows us to stick to our short deadlines. The technologies are not meant to be radically different from those that have been used to date; rather it is the way we will use the payload in achieving the mission’s over all aim – to study already discovered far away worlds – that sets Twinkle apart. The payload studies will be completed by the end of this year. From there we can start building!
N.B. Our very own Payload Lead, Giorgio Savini, is also working on a set of build instructions for a LEGO model of Twinkle. If you’d like to build our exoplanet explorer in brick, watch this space!
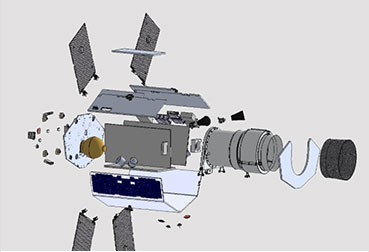